CONSTRUCTION OF A DAM EMBANKMENT WITH NONSTATIONARY QUEUES
Photios G. Ioannou
Civil & Environmental Engineering Department
University of Michigan
Ann Arbor, MI 48109-2125, U.S.A.
ABSTRACT
This paper presents the simulation model for a project
involving the haulage and placement of rip-rap for the
construction of a dam to illustrate how traffic-related
queues are created at locations determined dynamically at
simulation runtime. This example also investigates the
formation of moving queues of equipment that cannot pass
each and travel together like a procession or a convoy. The
solution to this problem is outlined conceptually using the
activity-scanning modeling paradigm and is described in
detail using a simulation model developed in
STROBOSCOPE.
1 INTRODUCTION
Applications of simulation modeling to civil engineering
construction and in particular to earthmoving often focus
on the interaction between dissimilar equipment, such as
loaders and haulers or pushers and scrapers. A typical
objective may be to model the resource-matching
complications introduced by having similar equipment of
various sizes and capacities, such as large and small
loaders and/or large and small haulers. Typically, hauling
and returning to load are modeled as simple activities
where the main difficulty is to estimate accurately the
distribution of the corresponding travel times.
There are cases, however, where the complexities in
an earthmoving project are due to interactions that occur
while the equipment are moving in traffic. These
phenomena are similar to those in transportation where
vehicles traveling on highways often form moving queues.
Neither the location of these queues nor the times at which
they form are predetermined. In such cases, simulation can
be used as a powerful tool to investigate traffic interactions
and to evaluate haul and return strategies.
This paper presents an example of this type of problem
that involves the placement of rip-rap for the construction
of the embankment for a dam. The primary difficulty in
this project is due to the interaction between loaded and
empty haulers that travel in a one-way road at the top of
the embankment without the ability to overtake each other.
Two construction alternatives are being considered:
- Build a new return road out in the water
beyond the edge of the embankment. - Use an existing road that takes trucks over a
longer route on the other side of the water
channel.
Equipment that the contractor plans to use include:
- Caterpillar 992B wheeled front-end loaders,
and - Caterpillar 772 tractors with 100-ton trailers
(converted from bottom-dump to side-dump).
To achieve the required production the contractor must
use two front-end loaders whose location within the
loading area is indicated in Figure 1. The required number
of haulers (tractor-trailers) as well as the preferred
construction alternative are to be determined.
Information about the performance of the front-end
loaders appears in Table 1. Similar information about the
haulers is shown in Table 2. The rip-rap material properties
are shown in Table 3. Table 4 shows project-wide cost
data. In these tables, the units LCY, loose cubic yards,
refer to the volume of material that has been broken up.
BCY, bank cubic yards, refer to the volume of material in
its original undisturbed or unbroken state.
Fast haulers must tailgate those in front that are slower
(forming moving queues) and queues of stopped haulers
occur whenever a hauler stops to dump and blocks the
haulers behind it.
A simulation model for this problem is presented using
the notation of STROBOSCOPE (an acronym for STate and
ResOurce Based Simulation of COnstruction ProcEsses).
STROBOSCOPE is a simulation language and system
designed specifically for modeling construction operations
based on three-phase activity scanning and activity cycle
diagrams. The STROBOSCOPE language is described in
(Martinez 1996). Example applications can be found in
(Ioannou & Martinez 1996a, 1996b, 1996c) and (Martinez
& Ioannou 1994, 1995, 1999).
2 DAM EMBANKMENT PROJECT
An earth-moving contractor is about to bid on a segment of
a project for the construction of a dam that involves the
haulage and placement of rip-rap on the embankment
opposite the generator outfall. The embankment extends
for almost two miles (10,000 ft.) and is within one mile of
the material borrow pit. A total quantity of one million
bank cubic yards (BCY) is to be taken from this pit and
placed along the embankment. Figure 1 presents a diagram
of the project site layout.
As shown in the figure, the haul road along the top of
the embankment is only wide enough for one truck. When
a truck is stopped for dumping, no other truck can pass that
position due to the narrow roadway. The proximity to the
adjacent residential area precludes a widening of this
portion of the road. Noise restrictions in the residential area
impose a speed limit of 25 mph for haulers and a maximum
of 10 operating hours per day.
The conditions set forth in the construction contract
specify that the rip-rap be spread uniformly and that no one
embankment area should receive appreciably more or less
material at any one time. Moreover, the work must be done
in 1,000 operating hours (100 days), which in turn requires
a production rate of 1,000 BCY/hr.
Model: Caterpillar 992B Wheeled Front-end Loader | |
Load per Cycle | |
Bucket Size, BS, (CY) | 10 |
Bucket Fill Factor, BFF | 65 % |
(poorly blasted with slabs/blocks) Load per Bucket, BS*BFF, (LCY) | 6.50 |
Loading Cycle Time | |
Basic cycle time (minutes) Adjustments (minutes) | 0.40 |
Materials (bank or broken) | +0.04 |
Common ownership of trucks and loaders | -0.04 |
Constant operation | -0.04 |
Mean loading cycle time (minutes) | 0.36 |
(Actual loading cycle time varies uniformly ± 12% from mean value | |
Breakdown Data (no major breakdowns) | |
Minor Breakdown (minutes) | 20 ± 15 |
Every (minutes) | 210 ± 100 |
Cost Data | |
Ownership hourly cost, ($/hr) | 140 |
Ownership hourly cost, ($/hr) | 160 |
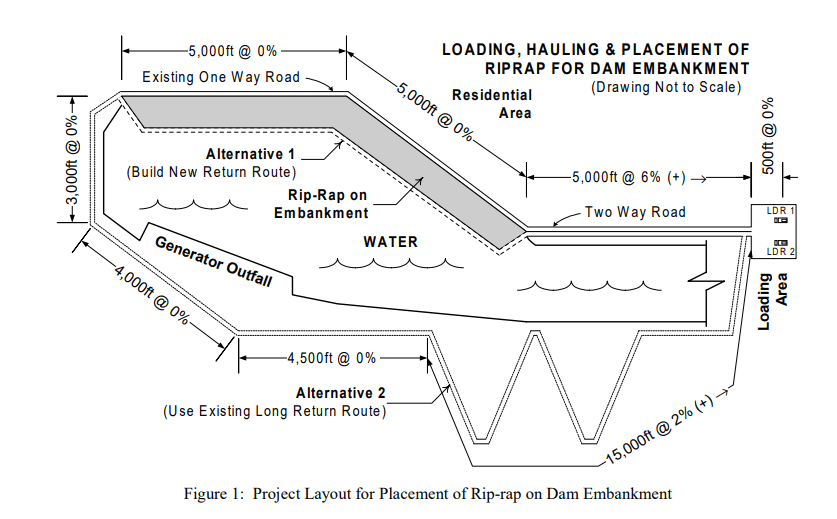
Model: Caterpillar 772 tractor and trailer
Size
Payload (lbs) 200,000
Length (tractor / total) 21′ 6″ / 65′ 7″
Width (tractor / total) 13′ 4″ / 15′ 0″
Loading height 12′ 4″
Times (seconds)
Dump time 50 ± 10
Spot time at loader 20
Pull-out time at loader 10
Acceleration
Loaded (0% grade): 0-25 mph 50
Empty (0% grade): 0-25 mph 35
Deceleration
Loaded (0% grade): 25-0 mph 40
Loaded (-6% grade): 25-0 mph 56
Miscellaneous
Travel time does not vary
Haul road surface – very hard, smooth,
watered (0″ tire penetration)
No altitude correction needed
No breakdowns
Cost Data
Ownership hourly cost, ($/hr) 50
Ownership hourly cost, ($/hr) 116
Large, broken pieces of granite (poorly blasted)
Unit weight
Broken, LCY, (lbs per LCY) 2,800
Unbroken, BCY, (lbs per BCY) 4,600
Load Factor (lbs per LCY / lbs per BCY) 61%
Amount of material to load and haul
Unbroken, BCY 1,000,000
Broken, LCY 1,639,344
Material per trailer load
LCY: (200,00 lbs) / (2,800 lbs/LCY) 71.43
BCY: (200,00 lbs) / (4,600 lbs/BCY) 43.48
Miscellaneous Costs ($ per 10-hr operating day)
General & administrative overhead 20,000
Liquidated damages (project T > 100 days) 20,000
Cost of new road for Alternative 1 ($) 500,000
2.1 Load Time Calculations
The time to load a hauler depends on its size relative to the
loader. As shown in Table 1, each scoop of material is 6.5
LCY. Since each hauler can carry 71.43 LCY, it takes 11
scoops to fill a hauler in 11 * 0.36 = 3.96 min. Adding 0.5
is moving or has stopped to dump (or because it is waiting
for a hauler in front to finish dumping).
The dumping sequence from site 0 to site 151 and
back again safeguards loaded haulers from having to stop
and wait prior to reaching their destination. The only
exception occurs when the hauler going to site 0 reaches
BOW while the previous hauler is still dumping at site 151.
In this case, it is possible to have a queue of loaded haulers
form at the entrance to the embankment.
Even though it is not possible to have a queue of
stopped loaded haulers within the embankment, it is
possible to have a queue of stopped empty haulers. This
occurs when the hauler in front takes too long to dump and
blocks the finished haulers behind it. The formation of this
type of queue is dynamic both in time and space and can
occur anywhere along the embankment.
When haulers cannot pass each other they tend to form
bunches (or moving queues) that travel together like a train
with the slowest hauler leading the group. When such a
train reaches the leader’s dumping site, all haulers are
positioned at their respective sites and can start dumping at
the same time. Thus, all haulers may finish dumping close
to the same time and this in turn creates the ideal
conditions for the formation of queues of stopped empty
haulers as described above.
2.4 Haul and Return Travel Times
The calculated haul and return travel times are shown in
Figure 2 using a cyclic activity-on-arrow network. This
network forms the middle loop in the figure and has event
nodes drawn as circles. As explained above, the inner loop
in this figure shows the route followed by the haulers,
while the directed arrows in the outer loop indicate the
distances in feet that the haulers must travel.
Of particular significance in this figure is the location
labeled Checkpoint. As loaded haulers leave the loading
area, they accelerate to 25 mph and continue for 2.45
minutes until they reach this point. There the driver must
decide whether to continue at 25 mph and proceed to the
dumping site, or brake and stop at the beginning of oneway (BOW) at the entrance to the embankment. These two
choices are shown in Figure 2 as “Go direct to site s” and
“Stop at BOW, then go to site s”. The location of the
checkpoint is 1,027 ft before BOW which equals the
braking distance traversed by a hauler during the 56
seconds (0.93 minutes) it takes to decelerate and stop from
25 mph at -6% grade.
The time in minutes for a hauler that continues past the
checkpoint (without stopping at BOW) to reach its
destination (dumping site s) is 0.80+0.03(152-s). The time
for a hauler that stops at BOW to reach its destination
depends on whether dumping site s is far enough for the
hauler to accelerate to a full 25 mph before it must
decelerate to stop and dump. If there is enough distance
from BOW to site s for the hauler to reach 25 mph (i.e., 0≤
s ≤127) then travel time equals 0.75+0.03(152-s). If site s
Combi activity BDArrivals represents the interarrival
time between loader breakdowns. At any given point in
time there is exactly one instance of this activity going on.
When BDArrivals finishes, it generates and places a
breakdown resource in queue BreakDownQ to allow
activity BreakdownTime to start and capture a loader from
LoaderQ. The captured loader is not available for starting a
Load activity until BreakdownTime finishes and the loader
is returned to LoaderQ where it becomes available for
loading haulers again
3.1 STROBOSCOPE Simulation Code
This section describes the statements for a complete model implemented in STROBOSCOPE to illustrate how the dynamics of this problem may be modeled in an activity scanning simulation system. First we define some parameters and global storage locations that are useful for sensitivity analysis:
Savevalues are storage locations that behave like variables in conventional programming languages. Here, NextSite stores the number of the site (0-151) to which the next loaded hauler will be assigned. SiteNBusy is a (0/1) flag indicating whether the dumping site at the entrance to the embankment is busy. SiteETA is an array with elements numbered from 0 to 151 that hold the arrival time of the last hauler to be assigned to the corresponding dumping site. The following types of resources are defined:
The first three resources are defined as generic resources because they do not need to be associated with any static or dynamic properties. Type Hauler defines a characterized resource type that has the property Payload. The only subtype of Hauler that needs to be defined is C772 with a payload of 200,000 lbs. Each resource of type Hauler has two saveprops (storage locations) called Site and LoadNo. Site stores the number of the site (0-151) to which the hauler must travel and dump. LoadNo is the serial number of the load carried by the hauler (1, 2, …)
The above on-start actions occur after an instance of
activity Haul2SiteFast has been created and its duration
has been determined. The first assigns to savevalue
SiteNBusy the value 1 (true), if the destination of the hauler
in this instance of Haul2SiteFast is site 151. Notice that
SiteNBusy is set at the start of Haul2SiteFast, i.e., at the
same simulation clock time that fork Checkpoint was
resolved last. Thus, the next time fork Checkpoint is
resolved SiteNBusy will indicate that site 151 is occupied
even though the hauler that will dump there may not have
reached its destination yet.
The second of the above on-start actions stores into the
corresponding Site element of array SiteETA the time when
the hauler in Haul2SiteFast will arrive at its destination. As
explained earlier, array SiteETA is used to prevent haulers
from overtaking their predecessors.
The duration of activity HaulToBOW is 0.93 minutes.
A hauler then enters queue WaitForLastSite where it waits
until activity Haul2SiteSlow can start. This occurs when its
semaphore becomes true, i.e., when site 151 is no longer
busy. As explained earlier, the duration of activity
Haul2SiteSlow depends on the distance the hauler must
travel to its dump site (i.e., whether Site<=127). Array
SiteETA is updated to indicate the hauler’s arrival time at
its Site as explained above.
The duration of activity Dump is uniform from 40 to
60 seconds. If the hauler is dumping in site 151 then at the
end of Dump, savevalue SiteNBusy is reset to zero to
indicate that the entrance to the embankment is no longer
blocked. Dump releases 43.48 BCY of Granite though link
GR2 that are deposited in queue RipRap. The current
contents of RipRap reflect total production.
2.2 Number of Dumping Sites
uniformly without any areas receiving appreciably more
material than others. An efficient way to achieve this is to
start at the west end of the embankment and have each
subsequent hauler dump its load immediately behind its
predecessor. When the entire embankment receives one
load from west to east, the process is repeated again. The
advantage to this approach is that loaded haulers can travel
to their destination without having to wait for the ones in
front to finish dumping. The only time loaded haulers may
have to stop is when a hauler dumps at the east end of the
embankment at the end of the cycle.
The distances that haulers must travel can be modeled
conveniently by dividing the length of the embankment
into equal dumping sites, each the length a hauler. Given
that the embankment is 10,000′ long and the length of a
tractor-trailer is 65′ 7″ we need 152 dumping sites.
A total of 1,000,000 BCY of rip-rap needs to be
placed, or 6,579 BCY per site. Since each hauler carries
43.48 BCY, each dumping site must receive 151 haulerloads. The entire project requires 23,000 hauler-loads.
2.3 Dynamic Queuing Behavior
A schematic showing the haul and return times for this
project appears in Figure 2. The innermost loop shows the
route that haulers must follow from the loading area (on
the right) to the embankment (on the left) and back. The
embankment (rip-rap area) is divided into 152 dumping
sites numbered from 0 to 151.
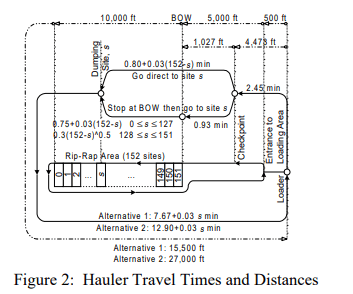
The point labeled BOW (Begin One Way) at the right
edge of site 151 indicates that the haul road at the top of
the embankment is narrow and can accommodate traffic in
only one direction. For the same reason, no hauler can
overtake another, irrespective of whether the hauler in front is too close to BOW (i.e., 128≤ s ≤151), the hauler
accelerates and immediately decelerates without reaching a
steady cruising speed and its travel time is 0.3(152-s)^0.5.
The time to return back to the loading area depends on
the location of dumping site s and the construction
alternative being modeled. For alternative 1 this time is
7.67+0.03s, and for alternative 2 it is 12.90+0.03s
3 SIMULATION MODEL
The activity-based network for the simulation model for
this problem is shown in Figure 3. At the start of
simulation the two front-end loaders are located in queue
LoaderQ and all haulers are in queue HaulerQ. Activity
Load is a combi (i.e., conditional) activity that can start
whenever LoaderQ and HaulerQ are not empty. When
Load starts it removes a loader from LoaderQ and a hauler
from HaulerQ. When it finishes it returns the loader to
LoaderQ and releases the loaded hauler to the normal (i.e.,
bound) activity Haul2CheckPoint.
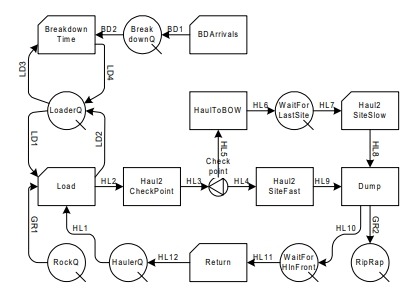
At the end of this activity the hauler proceeds to fork
Checkpoint where a dynamic decision is made whether to
continue through link HL4 or HL5. Link HL4 routes the
hauler to the normal activity Haul2SiteFast that models
traveling to the appropriate dumping site without stopping
at BOW. Link HL5 routes the hauler to the normal activity
HaulToBOW that represents the time it takes the hauler to
come to a full stop at BOW. At this point, the hauler enters
queue WaitForLastSite where it waits until the last site
(i.e., site 151) becomes free. When this occurs, combi
activity Haul2SiteSlow can start. At the end of
Haul2SiteSlow or Haul2SiteFast the hauler reaches its
destination site and continues with activity Dump. It then
enters queue WaitForHInFront where it waits until the site
in front of it is free and combi activity Return can start. At
the end of Return the hauler returns to HaulerQ and
completes its cycle.
of Granite from RockQ. Its duration is distributed
uniformly from 3.9 to 5 minutes, (i.e., mean = 4.46 min).
These strength expressions are logical opposites; when
one equals 1 the other is 0. Thus, even though forks in
general route resources probabilistically, Checkpoint
behaves like a decision node. A hauler follows link HL5
and stops at BOW, if there are any instances of
HaulToBOW currently going on (other hauler(s) in front
are about to stop), or there any haulers already stopped in
queue WaitForLastSite, or site 151 is busy. Otherwise, it
follows link HL4.
Since haulers cannot overtake each other, the time a
hauler arrives at its destination Site cannot be less than
the arrival time for the hauler in front. The modulo
division in the index of array SiteETA above ensures that
when Site is 0 we access SiteETA[151] (and not the
erroneous SiteETA[-1])
After Dump, a hauler enters queue
WaitForHInFront where it waits until all haulers in
front have finished dumping, too. The order of haulers
in this queue depends on their relative position along the
embankment and not on who finished dumping first.
This an important point because it is exactly the reason
why this queue is formed. When a hauler enters
WaitForHInFront it is positioned based on the queue’s
discipline which (as shown above) arranges haulers
based on LoadNo (or Site) with the smallest value in the
front of the queue.
A hauler cannot leave this queue until the enough
attribute of link HL11 becomes true (which is a
prerequisite for activity Return to start). As indicated by
the enough statement above, this occurs when there is at
least one hauler waiting in WaitForHInFront, and the
LoadNo of the hauler at the front of this queue is one more
than the number of Return instances this far. This would
indicate that the hauler in the front of the queue is the next
in line to return. The duration of activity Return depends
on the construction alternative (1 or 2) that is being
modeled
Since there are two front-end loaders, the limits for the
uniform distribution of BDArrivals (breakdown arrivals)
are divided in half. Its semaphore allows only one current
instance and then only when queue RockQ is not empty.
When there is no more Granite to load and haul the
simulation should stop (including breakdowns). The
priority of BreakdownTime is set high (above the default of
zero) so that when BreakdownTime and Load compete for
the acquisition of a Loader from LoaderQ,
BreakdownTime will be started first and draw the loader
and keep it out of work anywhere from 5 to 35 minutes.
These statements initialize the queues with resources
and start the simulation. The simulation ends when queue
RockQ becomes empty and there is no more rock to load
and haul. More complicated simulation control statements
can be used to effect multiple replications, common
random numbers, and other variance-reduction techniques.
The results shown in Table 5 and Figure 4 were collected
after a warm-up period of 3 hr based on 10 samples of 10
hr (separated by 2 hr intervals)
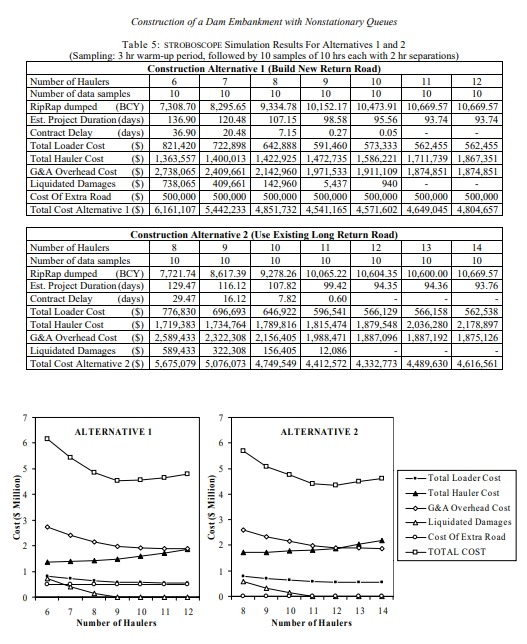
As shown by the STROBOSCOPE simulation results the
two construction alternatives are quite sensitive to the
chosen number of haulers. The optimum number of haulers
for alternative 1 is 9 and for alternative 2 is 12. This is as
expected since the haul and return cycle time for
alternative 2 is longer. The associated average total costs
are $4,541,165 and $4,332,773 respectively. Thus,
alternative 2 is preferred unless the cost for the new return
road required by alternative 1 can be reduced
4 CONCLUSION
The STROBOSCOPE model for this example can be expanded
relatively easily to produce an animation trace file for PROOF
Animation. This animation has been used to verify that that
the model is indeed correct, to investigate the effect of
various traffic policies and to present the results to others.
The layout for the animation is identical to Figure 1.
One of the shortcomings of animating this type of
problem is due to the need for geometric precision,
especially when representing the size of the haulers relative
to the length of the embankment. Since haulers must be
drawn 152 times smaller than the embankment, they appear
very small. Thus, it is best to view the animation on a large
high-resolution computer monitor.
STROBOSCOPE, its documentation, and several solved
examples are available at http://grader.engin.umich.edu andhttp://strobos.ce.vt.edu/
http://strobos.ce.vt.edu.
ACKNOWLEDGMENTS
The author wishes to thank the National Science
Foundation (Grant CMS-9415105) for supporting portions
of the work presented here. Any opinions, findings, and
conclusions or recommendations expressed in this paper
are those of the author and do not necessarily reflect the
views of NSF
REFERENCES
Ioannou, P.G. and J.C. Martinez. 1996a. Comparison of
Construction Alternatives Using Matched Simulation
Experiments. Journal of Construction Engineering
and Management, ASCE, (122)3:231-241.
Ioannou, P.G. and J.C. Martinez. 1996b. Simulation of
Complex Construction Processes. In 1996 Winter
Simulation Conference Proceedings. Institute of
Electrical and Electronics Engineers, Piscataway, New
Jersey, 1321-1328.
Ioannou, P.G. and J.C. Martinez. 1996c. Scaleable
Simulation Models for Construction Operations. In
1996 Winter Simulation Conference Proceedings.
Institute of Electrical and Electronics Engineers,
Piscataway, New Jersey, 1329-1336.
Martinez, J.C. 1996. STROBOSCOPE: State and Resource
Based Simulation of Construction Processes. Ph.D.
Dissertation, Department of Civil and Environ.
Engineering, University of Michigan, Ann Arbor, MI.
Martinez, J.C. and P.G. Ioannou. 1994. General Purpose
Simulation with STROBOSCOPE. In 1994 Winter
Simulation Conference Proceedings. Institute of
Electrical and Electronics Engineers, Piscataway, New
Jersey, 1159-1166.
Martinez, J.C. and P.G. Ioannou. 1995. Advantages of the
Activity Scanning Approach in the Modeling of
Complex Construction Processes. In 1995 Winter
Simulation Conference Proceedings. Institute of
Electrical and Electronics Engineers, Piscataway, New
Jersey, 1024-1031.
Martinez, J.C. and P.G. Ioannou. 1999, General Purpose
Systems For Effective Construction Simulation,
Journal of Construction Engineering and
Management, ASCE, (125)4, July-August.
AUTHOR BIOGRAPHIES
PHOTIOS G. IOANNOU is Associate Professor in the
Dept. of Civil and Environmental Engineering at the Univ.
of Michigan. He has received a Civil Engineer’s degree
from the National Technical University, Athens, Greece, in
1979; and a SMCE and Ph.D. in Civil Engineering from
MIT in 1981 and 1984. From 1989-1995 he has served as
Chairman of the Computing in Construction Technical
Committee of the ASCE. He co-developed the UMCYCLONE construction process simulation system with
R.I. Carr, supervised the design and development of
COOPS by L.Y. Liu, and chaired J.C. Martinez’s Ph.D.
dissertation on STROBOSCOPE. His research interests are
primarily focused on the areas of decision support systems
and construction process modeling